検索キーワードを入力
🏠 電気設備の知識と技術 > 電気設備設計の基礎知識 > 塩害地域と塩害対策・海岸からの距離
塩害対策の有無と海岸からの距離の関係
塩害とは、電気機器の表面や内部機器に対して、塩分を含む風や雨、汚れなどが侵入し、腐食や錆が発生する被害である。塩害によって盤類の表面が発錆してしまうと、電気機器の絶縁が劣化することになり、そのまま放置すると劣化部から塩分を含む外気や水分、虫などが入り込み、さらに腐食が進行する。
塩の影響は海に近いほど顕著となり、台風など風雨が強い時期には電気機器などに塩分を含んだ水分や砂などが飛散しやすくなる。沿岸部に近い場所に受変電設備や盤類、電線管などを設ける計画の場合、海から到達する塩分による影響を大きく受けるので、盤の表面塗装を塩害に強い製品とし、給気口には除塩可能なフィルターを設けて内部機器に塩分が付着しないよう対策を施す必要がある。
以下は、海岸線からの距離に応じて、塩害対策の基準となる地域を示したものである。
- 岩礁隣接地域:直接波しぶきがあたる場所
- 重塩害地域:海岸から200m~500m以内
- 塩害地域:海岸から2km以内
地域によって塩の届く距離に差があり、実際に飛来する塩分の量は海岸線の形状や風向、海抜高さなどで影響を受ける。海岸線から2km以上離れている場所であっても、強い塩害を受ける場所も存在するため、一概に何mから重耐塩とするか、耐塩とするかを判断することは困難であり、事業主との十分な協議が求められる。
対象地域の風向、近くに河川があるか、風が強い地域かといった多くの条件により、塩分の到達距離にも大きな差が発生する。建設予定地の周辺建物や既存建築物、既存工作物を観察し、塩害による発錆が起きていないかを調査するのも、事前確認として重要である。
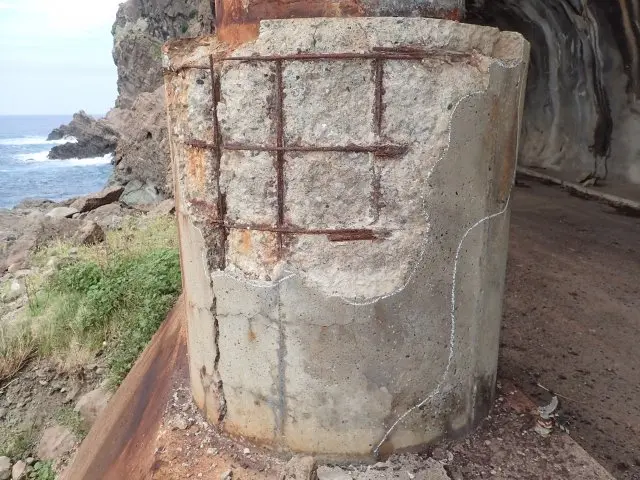
塩害による腐食が発生しやすい場所
塩害は、設備や配管などに対し、長期に渡って塩分を含んだ汚れが付着していると発生しやすい。そのため、軒下に設置された電気機器など、雨水による洗浄が行われない場所では、特に著しい腐食につながりやすい。雨によって洗われる環境は、直射日光による影響は大きい場所ともなるが、塩害対策としては定期的な洗浄の効果も考えられる場所ともなる。
軒下に設置されたキュービクル、分電盤、プルボックスなどは、塩分を含む風に晒されやすく、かつ雨によって洗われないため長期間に渡って塩分が付着したままとなり、腐食の進行が加速する場所となる。
しかし、雨に洗われることのみを設備洗浄として期待することはできない。定期的な発錆調査や洗浄、腐食が進んでいる場所の補修や再塗装を行い、腐食を早期に発見し補修することが、設備の長寿命化につながる。
外壁面に設置されるボックスなど、配線経路も同様である。定期的に雨水で洗浄される場所は比較的腐食しにくい環境であるが、配管やボックスの支持用ブラケットなどは、汚れが蓄積し腐食しやすい環境となる。他にも、雨樋の背面、基礎に接している盤のベースなど、汚れが蓄積する場所は塩分への接触機会が多くなるため、腐食がよりひどくなる傾向にある。
塩害地域に電気機器を設置する場合、定期的な拭き上げによる洗浄や、再塗装などこまめなメンテナンスが重要である。
塩害対策の基本事項
塩害対策の基本は「塩分から遮蔽すること」「塩分に晒されても問題ないよう絶縁を強化すること」「腐食に対して強化すること」の3つが挙げられる。
塩分から遮蔽する対策
電気設備を屋内に設置することが、最も単純でかつ効果的な塩害対策である。塩分に晒されない屋内設置であれば、腐食はほとんど現れない。電気設備を冷却したり、必要な換気を確保するために外気を導入する場合、塩分を含む外気をそのまま導入すると腐食が発生する。
塩分を含む外気が内部に吹き込み、内部機器に塩分が付着すると腐食の進行につながる。また塩分が含まれている汚れは、結露などで水分を含むなどして塩分が流出すると、本来絶縁されていなければならない充電部分の腐食、想定外の導通などが発生し、表面リークにより地絡や短絡事故につながる。
特に、沿岸地域では海に面した側の給気口から給気をすると、より濃度の高い塩分を吸い込んでしまうため、海側と反対方向から給気するなど、換気ファンやダクトの方向を調整すべきである。さらに、換気用のガラリやダクト中間に「除塩フィルタ」を設置し、導入する空気から塩分を取り除くことも検討すると良い。除塩フィルターを設置する場合、長期間使用するとフィルターが汚れることで静圧が増加し、換気風量が低下していくので、定期的な交換が必要である。通常、除塩フィルターは洗浄ができないので新品のフィルターに交換することとなる。
絶縁を強化する対策
塩害による被害を受けやすい部材の絶縁を強化し、汚れても不具合を起こさないよう施工するというのも塩害対策の一つである。高電圧充電されていたり、電柱の頂部などアクセスしにくい場所では、定期的な洗浄しにくいため耐塩碍子を使用したり、表面にシリコンコンパウンドを塗布するなど、絶縁部が強化された製品を選定することも、塩害対策のひとつである。
高圧電力の引込を行う場合、高圧気中開閉器(PAS)を設けることがあるが、事故発生時の波及事故は大きな被害を及ぼすため、絶縁不良に対してはより性能の高い製品を選定すべきものである。そのため多くの塩害対策品がラインナップされており、内部機器や機器表面の絶縁が強化されている製品が販売されている。
腐食を防止する対策
電気機器の表面に防錆性能の高い処理を行なったり、塩分が内部に侵入しないようフィルターで遮蔽することで、塩害対策とする方法である。分電盤やプルボックス、配管類・盤類は、鋼を用いて作られているため腐食の発錆を無視できない。腐食に強い溶融亜鉛めっきを施したり、耐塩性能の高い塗装を施した上で定期的に補修することや、素材をそもそも塩害に強いステンレス鋼にするなど、素材選定や塗装によって塩害対策を施すことが可能である。
なお、ステンレス鋼は耐塩性能が高いと考えられているが、SUS304の一般製品では、湾岸など海水が頻繁に付着する環境では簡単に腐食する。SUS316など、ステンレスの中でも海水に対して耐食性の高い製品を選定するのが重要である。
高い耐塩性能を必要とする場合、素材と塗装をともに耐塩仕様とし、かつ定期的な再塗装を施す必要が有るため、イニシャルコストだけでなくランニングコストが発生することに注意する。
キュービクルや分電盤の場合「配電盤類の塗装技術(JSIA-T1020)」を元にして塗装膜圧を決定するのが一般的な手法である。塩害地域の場合、外面40μm以上の表面膜圧を確保するが、品質管理上は60μm以上の膜圧を確保するのが良い。
外部からの塩害は材料や塗装によって保護し、機器内部の遮断器やリレー類といった精密部品は、そもそも塩分を含んだ空気を内部に流入させにくくすることで保護する。給気口には除塩フィルターを取り付けて塩分の流入を遮断し、長期にわたって利用したフィルターは汚損するので定期的に交換する。完全に塩分を遮断することはできないため、年次点検等で絶縁測定を行いつつ、充電部や盤内機器の清掃を行うことが重要である。
湾岸部に電気機器に対して、小屋を設けて塩分を遮断する方法もある。建築面積の増加となることや、軒下になることで雨による洗浄が期待できなくなるため、この場合でも定期的な点検や洗浄は不可欠と考えるべきである。
塩害地域での電気設備への対策
盤類や配管類への塩害対策の実例を紹介する。
盤類への塩害対策
盤類を塩害対策品とする場合、ステンレス製または、溶融亜鉛メッキ鋼板製とする方法がある。盤本体だけでなく、蝶番やボルト類も本体同種の金属とし、スイッチや表示灯、計器も同様に塩害対策品とする。違った種類の金属が接していると、異種金属接触による電位差が発生し、片方の金属が腐食してサビが発生するおそれがあるので、同種の金属を用いるのが安心である。
盤表面には、塩害に対して性能が確保できる塗装膜厚を把握し、規定以上の数値の厚さが盤の端部や天板、内部を含む全面に確保されていることを確認する。膜厚を未確認のまま盤類を現場に持ち込んでしまうと、塗装不足を現場搬入後に現地補修で改善すること自体困難であり、工場に持ち帰って再塗装しなければならず負担が大きい。
搬入済みの盤類を、塗装のために工場に持ち帰るのは現実的ではないため、できる限り工場検査にて膜厚を確認し、搬入前に仕様が適切であるかを確認すると良い。
盤に換気口がある場合、換気によって盤内部へ塩分の侵入が考えられるので、給気口に除塩フィルタを設けることや、給気口を海側の面ではない方向にする、空気の流通部をフィルター部に限定するために、ケーブルを接続するための配管は密閉するといった対策を施す。
盤表面の傷によって耐塩塗装が損傷すると、損傷部分を起点として腐食が進行するので、搬入据付時に傷が付かないように十分な養生を施すと良い。盤への配管用穿孔や、付近で配管切断などによって発生した切粉が付着していると、もらいさびの原因となるので、施工管理にも十分な配慮が必要である。
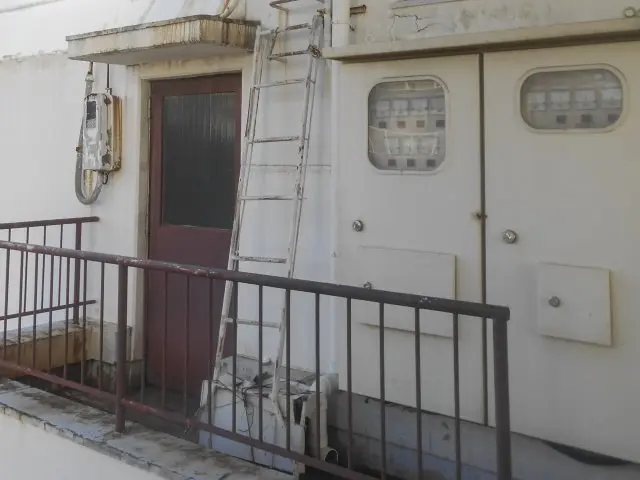
配管やケーブルラックの塩害対策
塩害地域内では、盤類だけでなく、プルボックスやケーブルラック、金属電線管なども全て塩害を受けるため塩害対策品としなければならない。盤本体の素材を腐食に強化されたステンレス合金や樹脂とすることが簡易な方法であるが、ステンレス鋼はイニシャルコストが大きく、樹脂は日射や衝撃に弱いため設置場所が制限される。多くの場合、溶融亜鉛メッキを施した鋼製材料を使用し、塩害の必要性に応じて耐塩塗装を施す方法が一般的である。
塩害地域で接続するケーブルや電線は、被覆の剥ぎ取りを最小限に留めることで塩害の影響を最小限としなければならない。導体への塩害を防止するため、テープ巻きや絶縁カバーを十分に設け、塩分を含んだ水分が侵入しないよう施工することが重要である。塩分を含む水分が導体部に侵入すると、絶縁破壊につながってしまうため注意が必要である。
塩害地域外であっても対策が必要
台風など、強風が吹いた場合には、沿岸地域でなくても強風によって塩分が飛散し、塩分による被害が広範囲に及ぶおそれがある。塩害地域の範囲外であっても、自然現象による塩害が発生することがあらかじめ判明している場合、地域外でも塩害対策を検討すべきである。
しかし、それにより設備投資が過大となることも懸念されるため、一時的にシートなどで電気設備を覆い、塩分を含む風の吹き込みを防止する方法も考えられる。コストなどの理由で電気機器を塩害対策品としない場合、定期清掃の頻度を高め、機器表面を清浄な状態に保つことで、腐食発生を低減できる。
塩害による事故は、塩分が電気機器や充電部に付着し、結露や雨水によって塩分が溶け、表面に導通部が構成されることにある。機器が定期的に清掃され、塩分を除去して汚損部分がなくなれば、結露や雨水が付着しても事故とはならない。
定期的な清掃は塩害対策として有効であるが、結露などによる汚損を発生させないという考え方も塩害対策のひとつとして有効である。盤内の結露を防止するには、機器内の急激な温度変化を防止することが効果的なため、分電盤内部に結露が懸念される場合は、分電盤やキュービクルの内部にスペースヒーターを設置して盤内温度を上昇させるといった対策を行うと良い。
照明器具の塩害対策
屋外に設置する照明器具も、沿岸部に近い場合は塩害対策品を選定しなければならない。照明器具本体や照明ポールは、本体に塩害対策の塗装をしたり、ステンレスにするといった対策を実施する。
照明器具の場合、一般的に重耐塩と耐塩の二種類のグレードで検討するのが一般的である。器具本体はステンレスや溶融亜鉛メッキ製とし、アクリル樹脂系塗装やポリウレタン樹脂系塗装を表面に施した製品がよく選択される。器具本体の塗装だけでなく、ボルトや支持金具なども耐塩性能の高いステンレス製や溶融亜鉛メッキ製を使用する。
照明器具の施工中や、運搬中に付いた傷からも腐食が大きく進行するため、傷ができた場合は速やかに補修する。照明器具を接続するソケット部は、発錆するとランプが抜けなくなることがあるので、期待寿命が短くなることを想定する。
軒下に防水器具でなく一般器具を設けると、本体のほか接点部分が早期に腐食するので、耐候性の高いパッキンが付属している製品を用いるよう配慮するべきである。
照明器具の耐塩塗装
照明器具の耐塩塗装を考える場合、照明器具本体の耐塩塗装と、ポールの耐塩塗装をそれぞれ別に検討する。
器具本体はメーカーの工場で所定の塗装を施して納品するのが一般的であるが、ポールについては現場塗装という選択肢もあり、メーカーでは搬入用の錆止め塗装までとし、現場搬入後に塗装することもある。照明ポールの素材はSUS304として、アクリル樹脂系塗料、ポリウレタン樹脂系塗料、ポリエステル樹脂系塗装、エポキシ変成メラミン樹脂系塗装を上塗りするといった対策がある。塗膜の硬度や耐塩性の高さ、白亜化への強さを考えて、アクリル樹脂系塗装の選択が多い。
溶融亜鉛めっきを施した照明ポールに、さらに塗装するという手法もあるが、下塗りを十分に行わないと剥離するので注意を要する。
照明器具の塩害対策施工における注意点
照明器具や照明ポールは、盤類と同様に、雨に洗浄されない場所に設置すると腐食が進行しやすい。屋根の下に自立照明を設置した場合、定期的な洗浄により塩分を洗い流さなければ腐食につながる。
照明器具のソケット部は、塩分の付着によって絶縁低下を引き起こし、腐食により電球の電極部分が癒着することがあるため、定期的な清掃や、交換頻度を高める措置が必要である。
密閉タイプの照明器具の場合でも、開閉機構やパッキンの腐食が進行するので、耐候性に優れた製品を選定することが重要である。腐食が進行していると、メンテナンス時に開閉機構が動かなくなったり、パッキンが腐食して内部漏水することも考えられる。